2023.10.03
内径加工やチップについて
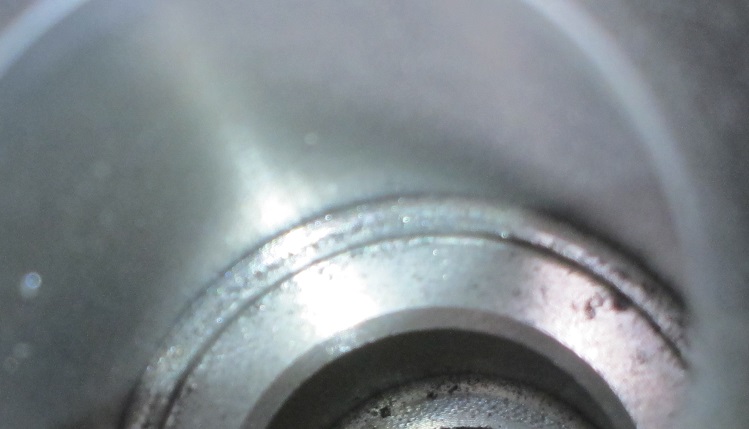
先日、改善後の立ち会いフォローに訪問しました。
削りの動きの最適化、チップ・切削条件の見直し、工具数削減が主な改善点です。
機械剛性など個々に違いますので、最終的には切削音や出来映えを見ながら切削条件を詰めていきます。
内径加工は工具剛性が重要ですので、出来るだけ太いボーリングバーを使用したい所ですが、ワーク形状の制約があります。
さらに剛性を上げるために超硬防振バーに変更をしたり、チップをネガからポジに、M級からG級に変更、低抵抗のブレーカーに変更をするなどの工夫も必要ですが、図面要求に対して過剰スペックになってはもったいないです。
出来るだけM級のネガチップで、削りしろに合った低抵抗のチップを見つけることにより、ランニング工ストを抑える事が出来ます。
もちろん工具寿命に大きく影響するチップの材質も重要です。
柔らか過ぎると寿命が短く、硬すぎても欠けやすくなります。
多くの現場で感じる事が、切削条件が突き詰められていないこと。
ワークの材質や削りしろに合わないチップ材質やブレーカーが使われていることも少なくありません。
また一度立ち上げを行うと、プログラムや工具が見直されていないことも多くあります。
チップも日進月歩で進化しております。
今期の話ですが、チップの寿命改善で各メーカーの適したチップを9種類テストし、結果的に寿命が2倍以上となり年間効果金額が60万円以上の削減となった製品もありました。
数種類のチップテストは手間も時間も掛かりますが、生産性向上や工具費削減にはとても重要です。
①切削条件を突き詰めて、最適な条件の見極める
②使っているチップが本当に最適なのか?を疑い、サンプルテストの実施
切削加工現場は改善の余地がたくさんあり、追求をすればノウハウとなり収益にも繋がります。
是非①②の改善を頂きたいと思います。